Ever wondered how intricate car parts, engine blocks, or electronic casings are made? Discover how die casting manufacturers turn concepts into finished products with precision and expertise.
The die casting process rapidly transforms molten alloys into high-quality parts by injecting them at high pressure and speed into metal mould cavities, known as ‘dies.’

DIE CASTING ADVANTAGES
High Quality & Customization
Unique parts can be produced to meet customer specifications, allowing for the creation of components tailored to complex geometries and specific needs. Corrosion rates for die castings are slower than those for sand castings due to the smoother surface. Die casting parts for various applications can be achieved with advanced technology and precision machinery.
Versatility & Accuracy
The die casting method produces intricate parts with high accuracy by utilising CNC machining to create the die. This process adheres to stringent standards such as ISO 2768, which helps manufacturers maintain uniform dimensional accuracy. ISO 2768 specifies tolerance values for acceptable variations in machined parts, ensuring consistency and quality. The precision of a part can be significantly increased by using CNC machining after the casting process.
Time & Cost Efficiency
The die casting process efficiently saves time and resources by quickly producing large quantities of parts. It streamlines production through reducing or removing secondary machining, and ensuring high repeatability. The simplicity of die-cast manufacturing lowers the incremental cost per item, making it well-suited for large-scale production of small to medium-sized castings. It conserves material and allows developers to reduce production costs while upholding high-quality standards.
Miscellaneous
Die casting parts enable the embedding of inserts such as threaded inserts, heating elements, and high strength bearing surfaces during casting. Unlike permanent moulds and sand castings, die casting fluidity is unaffected by the solidification range.
DIE CASTING CHALLENGES
The design and quality of the die casting mould is crucial to the overall casting quality. A poorly designed or low-quality mould can result in defects such as incomplete filling, shrinkage, and warpage.
Temperature and Humidity Control
Temperature and humidity during casting significantly impact quality, influencing defects like porosity, surface roughness, and cracks. Porosity refers to the presence of pores or gas bubbles, which can obstruct heat treating or welding. Trapped gas can expand during heating, causing micro-cracks and surface flaking. Incorporating vents along parting lines helps mitigate these issues.
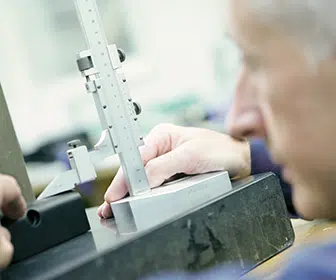
Process Control
Each stage of die casting requires precise control to ensure the best possible quality of the cast. This means a stringent process control system in which every stage is monitored and controlled is a must for high-quality casts.
Surface Finish
The surface finish of the casting is critical as it affects both its appearance and functionality. A subpar surface finish can result in defects such as irregularities, roughness, and unevenness.
Capital Cost
Die casting equipment, mould creation, and casting materials all require significant upfront costs. However, for large production volumes, die casting is more cost effective compared to other methods such as SLS or CNC machining.
RELIABILITY AND EXPERTISE WITH ARRK ASIA
ARRK Asia has built a reliable reputation in the die casting industry for many years. Our team of experienced professionals are highly skilled and knowledgeable in the die casting process, enabling us to help customers prevent and minimise potential challenges during manufacturing. We utilise advanced simulation software to analyse and optimise every aspect of the casting process to reach high quality standards for our customers.
Seeking expert guidance to produce high-quality parts? We’re up for the challenge! Contact us today for a quote!