Discover why vacuum casting services stand out as one of the top choices for medical device development. Vacuum casting is a manufacturing process in which molten material, commonly polyurethane rubber, is poured into silicone moulds created from a master mould. It is a popular casting process for making prototypes and samples during the early stages of product development before committing to injection moulding.
MEDICAL DEVICE DEVELOPMENT
- Material Requirements
- Medical devices and equipment must be biocompatible, ensuring they are non-toxic, non-allergenic, and non-irritating, especially those in direct contact with the human body. It is important that parts such as grips, gaskets, seals possess good strength and resiliency. Flame-retardant properties are also essential for ensuring safety.
-
- Biocompatible materials commonly used in vacuum casting include:
- Polyethylene (PE)
- Polypropylene (PP)
- Polymethylmethacrylate (PMMA)
- Polyvinyl Chloride (PVC)
- Biocompatible materials commonly used in vacuum casting include:
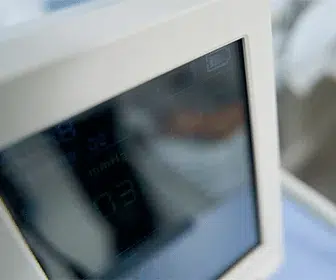
- Quality Requirements
- Medical devices are involved in the diagnosis, monitoring, and treatment of diseases. This means that the product quality must be exceptional, no errors are to be tolerated in the end product.
- Regulatory Requirements
- All medical products or equipment must go through strict reviews and regulatory checks before it can be accepted for clinical use in the market. The most common standard to follow is ISO 13485. Therefore, tolerances should have acceptable safety and performance standards.
- Budgetary Limitations
- Research and development of medical devices require significant funding, but budgets are often constrained as they need to be allocated across multiple areas. Prototyping costs are important, but if too high, they could restrict funds for other critical areas such as research and testing. Reducing prototyping costs is essential to maximise budget allocation, but high-quality prototype fabrications are often quite costly.
- Low Volume
- During the product development stage, producing high volumes is unnecessary. Instead, a small batch of 10 to 50 units is sufficient for dimensional and functional confirmation as well as testing. However, this low volume does not qualify for the most cost-effective mass production methods.
- Time Constraints
- The competition is fierce in the field of medical devices, as it is with all other industries. Therefore, speed to market is one of the key factors to successful product release.
There are many more challenges in medical equipment development, the ones highlighted are particularly significant. ARRK Asia leverages its expertise to tackle these hurdles, recognizing that seemingly minor issues can accumulate over time.
Our vacuum casting services ensure materials meet stringent standards. To prevent roadblocks later, it’s important to address these challenges head-on with our team’s expertise.
BENEFITS OF VACUUM CASTING
- High Dimensional & Visual Accuracy
- Vacuum casting services use silicone moulds made from a master model, which serves as the first prototype part. The master model is commonly produced through 3D printing or CNC machining to ensure it remains extremely faithful to the original design, both structurally and visually. When the master model is accurate, all subsequent vacuum-cast parts will be identical to the prototype design.
-
- Vacuum casting utilises a variety of materials such as thermoplastics, rubbers, and resins. Vacuum casting parts can be produced with varying degrees of the following attributes and characteristics:
- Physical Appearance & Colour
- Impact Strength & Hardness
- Flame Retardant Capabilities
- Electrical Properties
- Chemical Resistance
- Vacuum casting utilises a variety of materials such as thermoplastics, rubbers, and resins. Vacuum casting parts can be produced with varying degrees of the following attributes and characteristics:
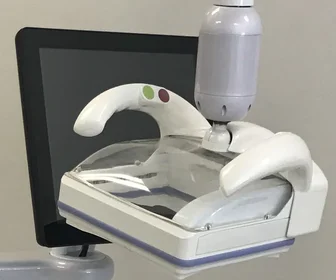
- Cost Efficiency
- Although vacuum casting has a higher setup cost compared to other types of casting, it is more cost effective in cases where a low volume of products (between 10 to 50 units) is required.
- The cost typically falls between that of 3D printing or CNC machining and mass production as individual manufacturing processes. Vacuum casting manufacturers offer an excellent solution to bridge the gap between prototyping and mass production.
- Silicone moulds lower the cost of multiple product iterations, as they are cheaper than the metal moulds used in injection moulding. This can be game-changing, as many prototypes undergo several design changes to adapt quickly to shifting market dynamics.
- Agility & Flexibility
- The creation of silicone moulds is much quicker compared to the creation of metal moulds. This results in shorter lead times, which facilitates faster product development and rapid market access. Additionally, it allows product developers to make changes and prototype iterations of their product more easily and rapidly.
- Risk Management
- As a low-volume manufacturing method, vacuum casting lowers the financial risk of parts production, as it does not require the significant initial investment and commitment of mass production. If an issue is found, the resulting loss will be much smaller compared to an error discovered after committing to mass production.
As evident from the listed benefits, vacuum casting provides an effective solution to address challenges faced by medical equipment developers.
LIMITATIONS OF VACUUM CASTING
- Zero Room for Error
- The master model will be used to create the mould, any defects or inaccuracies while making the master model will reflect on all subsequent parts. Therefore, it is necessary to have a near flawless master model in order to produce the best results.
- Shrinkage
- Due to the thermal expansion of the liquid material and the softness of the silicone mould, the final products typically exhibit a shrinkage rate of 0.15% to 0.30%. Although this rate is lower than that of injection moulding, it can still be significant if the parts are to be assembled afterward, potentially leading to gaps or unwanted spacing between the joined parts.
- This effect is particularly noticeable in parts with irregular shapes or varying wall thicknesses. However, proper calculations and specific design modifications, such as adjusting rib thickness, can help minimise this issue.
- Mould Depreciation
- The softness and flexibility of silicone moulds has an inability to maintain shape over extended use. They typically last for approximately 10 to 25 parts, depending on the complexity, size, and material of the parts. moulds degrade faster when producing larger parts with rough surfaces and prominent features, compared to smaller, smoother, and less detailed parts. Proper maintenance and careful design considerations can help extend mould life.
- Design Limitations
- Although vacuum casting parts can be thin, the recommended wall thickness ranges from 1.5 mm to 4 mm, with an absolute minimum of 1 mm. Parts thinner than 1 mm are highly prone to breakage. Additionally, sharp edges, corners, or intricate details will typically appear rounded after casting. Certain features may also require the use of plugs and cores during the casting process.
- Temperature Limitations
- Vacuum casting materials simulate plastics or rubbers, parts made using this method are not suitable for applications that involve high temperatures.
- Surface Finishing
- Surface finishing on vacuum casted parts is carried out during post-processing. This process is often limited to the part’s exterior, as accessing internal features, especially those with deep cavities, can be quite challenging.
These limitations can be mitigated or avoided by collaborating with ARRK Asia’s experienced and knowledgeable team.
WHY SHOULD YOU CHOOSE ARRK?
In the medical industry, ARRK has been instrumental in developing products such as airway management devices (laryngeal masks) and oscilloscopes. However, our primary expertise lies in prototyping enclosures for medical devices, typically crafted from plastics or metals.
We recognize the importance of communication and collaboration between the prototyping and development teams. Understanding product design specifications and intent is crucial, as it ensures that prototypes align closely with your vision, resulting in superior outcomes.
ARRK Asia combines expertise, cutting-edge technology, customizable solutions, and a well-established global reach. We are fully equipped to assist you in producing high-quality medical equipment prototypes efficiently, without compromising on cost or time.
Get a quote and start your project today!