The team of ARRK Asia has used aluminum casting as an advanced manufacturing process to help companies produce high-quality, durable products with great efficiency and low cost. What is aluminum die casting process? For manufacturers, it has worked to create parts out of mild steel, stainless steel, titanium, or even other materials such as cobalt-chrome and nickel silver.
Aluminum Die Casting Process
Aluminum is a metal commonly used in manufacturing products today because it is lightweight, strong, durable, and corrosion-resistant. In addition to these advantages, aluminum offers many environmental benefits since it is easily recyclable, which decreases landfill space and reduces greenhouse gas emissions.
Aluminum Die Casting is a manufacturing process wherein molten metal flows through a mold under pressure, creating a cast product identical to the original mold design. The material properties of Aluminum Die Castings are similar to those of wrought iron, except they are much stronger and less brittle. These materials are used in automobiles, appliances, electrical components, machinery, and hardware.
Aluminum Die Casting equipment and methods
The aluminum die casting process uses equipment, tools, and methods specifically designed to produce quality castings. When choosing the appropriate method for your project, consider important aspects such as size, complexity, number of pieces, and cost.
Therefore, the aluminum die casting process is used to create parts that require high precision. The main reason ARRK uses die-cast aluminum to manufacture parts is the possibility of a tighter dimensional control than cast iron and steel, making them suitable for medical devices. In addition, compared to injection molding, the die-casting process creates a stronger part due to its superior surface finish.
Injection Molding
Injection molding uses plastic pellets and pressure to fill molds. Plastic is heated and injected into a mold where it cools and solidifies. Parts produced using this method have poor surface finishes and may crack or break if subjected to high temperatures.
Die Casting
Compared to injection molding processes, die casting produces a higher quality product with excellent surface finishing. Instead of heating plastic before injecting it into a mold, die casting requires molten metal to enter a cavity. The metal then hardens after cooling. As a result, parts produced via this process are generally stronger than those produced by injection molding.
Advantages of Aluminum Die Casting
- High-Quality Surface Finish: Part surfaces formed through die casting are smooth and free of scratches and blemishes.
- Stronger Than Injection Molded Parts: Due to their composition, die-cast parts tend to be stronger than molded parts. As a result, they are able to withstand greater forces without cracking or breaking.
- Better Tolerance Control: Because die-cast parts are manufactured under controlled conditions, they offer higher accuracy and uniformity.
- Less Material Waste: Since aluminum is recycled frequently, less material ends up being wasted.
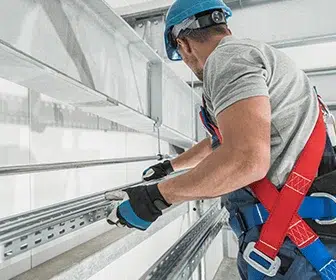
With these techniques, ARRK Asia has helped many companies with precision-engineered components and assemblies. These applications include industries such as aircraft, automotive, medical, electronics, architectural, chemical mechanical, food processing, etc.
Today’s die castings are incredibly durable, strong, lightweight, and corrosion resistant, making them perfect candidates for applications involving extreme temperatures, durability, high pressure, and long service life.
If your company needs expertise in the aluminum die casting process, or any rapid prototyping rapid prototyping or low volume production manufacturing process, contact ARRK Asia’s team for a customized solution for your project.