What is thixomolding? Thixomolding is an interesting phenomenon where an object gets a smooth surface after melting. When something is thixomolded, does it mean it is molded using plastic or metal? The answer is both! In this article, we will discuss more about it.
Thixomolding and its manufacturing procedure
In the manufacturing industry, thixomolding is a technique involving the application of heat at low pressures to form materials into desired shapes and forms. The method was developed from plastic injection molding.
Thixomolding has become widely adopted in the automotive, aerospace, medical device, packaging, and consumer goods industries.
It involves heating molten material until it reaches its glass transition temperature (below which it becomes pliable), then injecting it into a mold cavity and allowing it to cool slowly or rapidly. This cooling process creates a solidified part that resembles the original shape of the mold.
In component manufacturing, ARRK Asia has an amazing capability to use thixomolding to form parts.
Advantages of materials used in thixomolding
Thixomolding is a particular type of plastic molding technique where polymer material is mixed with small particles to produce a strong and lightweight product. It is primarily used in manufacturing equipment, structural, and automotive parts.
Thixomolding uses a mixture of two different plastics, polypropylene (PP) and styrene-butadiene rubber (SBR). ARRK Asia has several types of PP/SBR blends depending on the type of injection molding needed. Our plastic components are molded using a machine called a screw extruder and then pelletized.
This process has many advantages over traditional injection molding, including reduced cycle time, lower cost per unit, improved product characteristics, ease of automation, superior temperature tolerance, and increased mechanical integrity.
Each material has its own set of pros and cons, however. Here’s a brief overview of each plastic.
Polypropylene
Pros
- Low cost
- Widely available
Cons
- Limited chemical resistance
- Poor color retention
Styrene Butadiene Rubber
Pros
- High tensile strength
- Excellent electrical insulating properties
- Good dimensional stability
- Easy cleanability
Benefits of thixomolding
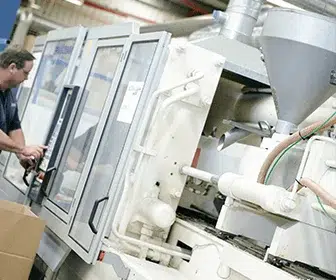
Manufacturers have been using these plastics for building cars since the 1940’s, but they weren’t widely used until the 1980’s. Since then, thixomolded products have become increasingly popular due to their low cost, high quality, and durability.
Thixomolding is widely used today in making car bumpers, door panels, dashboards, headlamps, hoods, fenders, wheel covers, and roof trims. Nowadays, other industries like aerospace, medical, electronics, dental, and food processing use thixomolding.
There are several advantages of using thixomolding over traditional methods in producing molded products, such as lower costs resulting from reduced labor requirements and fewer raw materials. Another advantage is the time savings associated with lowering mold cycles and shorter cycle times.
ARRK Asia can produce high-quality molded products that are thixomolded, suitable for applications requiring higher temperatures than conventional injection molds.
Furthermore, thixomolding reduces the need for post-molding operations such as painting, plating, and coating, making it one of ARRK’s important production methods.
The application of coloration to molded parts is possible if the manufacturer follows strict procedures, avoiding any undesirable discoloration. In addition, thixomolding helps reduce hazardous wastes in the environment. It eliminates metal scrap and avoids the use of toxic chemicals.
Contact ARRK’s team for further information about the low-volume inject molding in Asia solutions it can provide to your production project.