In today’s fast-paced market, the speed of a new product to market can make all the difference. Rapidly turning design concepts into tangible prototypes is essential for speeding up development and reducing time-to-market.
Curious about why Computer Numerical Control (CNC) machining is essential in this process? Discover why it’s a game-changer for rapid product development.
WHAT IS CNC MACHINING?
CNC machining is a manufacturing process that uses computer-controlled machine cutting tools to precisely material from a block, known as a workpiece. This ensures that the prototype closely mirrors the original design.
Unlike traditional manufacturing methods, which may require extensive tooling and setup, CNC machining operates with minimal lead time for rapid prototyping. It enables quick iterations and adjustments. This capability is crucial in the early stages of development when changes to the design are frequent.
The process begins with creating a 3D Computer Aided Design (CAD) model of the final product, which is then converted into Computer Aided Manufacturing (CAM) files. These CAM files generate the G-code that directs the CNC machine, ensuring efficient and precise prototype production.
ADVANTAGES OF CNC MACHINING
High Accuracy and Precision
CNC machining uses computer programs to control cutting tools with exceptional accuracy, interpreting CAD files into precise machine instructions. High-resolution encoders and feedback systems provide real-time data, ensuring tight tolerances, often within ±0.01 mm, and the ability to create complex geometries and fine details. The rigid construction of CNC machines minimises deviations, while 3-axis and 5-axis capabilities allows undercuts, cavities and intricate designs. The machines deliver remarkable precision, achieving such accuracy often involves investing in high-end equipment.
Material Versatility
CNC machining materials are highly versatile, offering a wide range suitable for producing both simple and complex parts. This flexibility makes it an ideal choice for various industries, from automotive, aerospace to consumer electronics and medical devices. Plastic is a popular CNC material due to its versatility, lightweight nature, and ease of processing. Different types of plastics, such as ABS, polycarbonate and acrylic, can be machined to create parts with specific properties.
Metal is one of the most common materials that offers strength, durability, and the ability to withstand high-stress environments. Metals like aluminium and steel are frequently machined. The flexibility to work with materials closely resembling actual production materials makes it invaluable across various industries.
Speed
CNC machining speeds up development by bypassing moulds and preliminary steps, producing parts in days or hours. It supports iterative design by enabling quick modifications and re-machining if there is early detection of design flaws.
The use of cnc material blocks similar to production materials ensures prototypes are accurate, providing a reliable preview of the final product and reducing overall lead times for production.
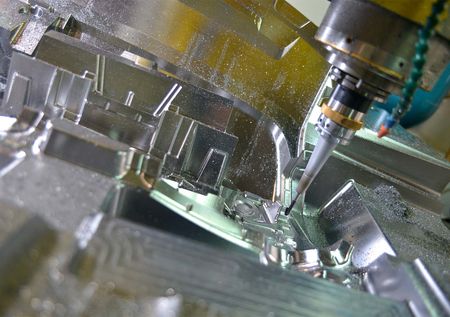
Cost-Effective Prototyping
CNC machining combines precision and speed with cost-effectiveness, making it an accessible option for prototyping across businesses of all sizes. By eliminating the need for costly fixed tooling and moulds as the upfront expenses for iterations of tooling. Once a CNC machine is programmed, it operates with minimal manual intervention and ensures consistent quality and precision across multiple prototypes.
CNC machines are built for durability and typically require less maintenance than manual equipment, which helps lower long-term operational costs. While the initial investment is higher compared to 3D printing, the CNC process offers superior accuracy and a wider range of materials. Although high upfront costs can be significant, the long-term advantages of its speed and precision generally justify the investment.
Consistency and Repeatability
CNC services are highly scalable, making it an efficient solution for producing parts in both small and large batches. Its ability to deliver consistent quality at scale reduces the per-unit cost, making it a competitive choice for larger orders. This process is typically lower than processes like injection moulding, which can be costly for smaller production runs
CNC machines excel at swiftly switching between various designs and materials, making them ideal for producing limited runs of customised or experimental parts. Once set up and programmed, they ensure the production of identical parts with consistent quality and repeatability. The automation involved helps minimise human error and guarantees reliable results across multiple parts.
LIMITATIONS OF CNC MACHINING
High Initial Setup Costs
The initial cost of CNC machines and their setup can be substantial, especially when factoring in accessories like specialised cutting tools, fixtures, and cutting fluid delivery systems. Beyond the machine itself, businesses must also invest in high-quality software, such as CAD and CAM programs, for programming and control.
The proper infrastructure to operate CNC machines requires reliable power supply and ventilation. These systems ensure smooth operation, especially when the machine runs continuously for hours or even days, depending on the complexity of the parts being produced. ARRK has years of experience in CNC machining services, helping to bypass high upfront costs by providing access to both 3-axis and 5-axis CNC machines.
Technical Expertise
CNC programming must be detailed and precise to produce parts, a process that can be both complex and time consuming. Skilled operators or programmers are essential for creating and managing CNC programs, including designing CAD files and generating CAM files. They must also be trained in setup, operation, and testing procedures, requiring experience and innovative approaches.
The complexity of this process, along with the time investment, can be a challenge for small-scale operations or projects with limited budgets. ARRK’s teams equipped with skilled personnel ensure benefits from long-term efficiency and quality.
Geometric Restrictions
This process limits the production of certain complex designs as it involves material removal from a solid block. In contrast, an additive process such as 3D printing builds parts layer by layer, enabling the creation of detailed internal geometries and typically at a lower cost.
While CNC machining may incur higher material costs compared to the filament or resin used in 3D printing, it offers superior precision and a broader range of materials, making it a valuable choice for projects requiring accuracy and durability.
Material Wastage
CNC machining is a subtractive manufacturing process that involves removing material blocks, until the final product is shaped. This process often generates considerable amounts of scrap metal or plastic. The initial iterations are not satisfactory, the cost and material waste can quickly increase due to repeated attempts.
ARRK’s expertise helps mitigate these challenges by guiding clients in selecting the optimal workpiece size and refining 3D data before machining begins, reducing both material waste and unnecessary costs.
Care and Maintenance
Like other advanced machinery, CNC machines require regular maintenance to operate at peak performance. Malfunctions can lead to damaged parts, costly repairs, and production downtime. The tools used in machining also need periodic replacement and upkeep to ensure minimal wear and maintain optimal precision.
These maintenance needs contribute to operational costs, but they are essential for preserving the machine’s accuracy. At ARRK, our skilled team manages these maintenance tasks efficiently, ensuring consistent quality and reliable parts for our clients.
ARRK OFFERS CNC MACHINING SERVICES
CNC machining is a cornerstone of rapid prototyping and product development and will continue to be an essential tool in bringing ideas to life.
With over 70 years of experience in CNC machining, ARRK Asia is well-equipped to overcome limitations and manage complex projects swiftly, helping clients meet tight deadlines and streamline development processes.
Discover how ARRK Asia can enhance your project’s efficiency and quality. Contact us today to discuss your needs and experience our superior CNC machining services.