In recent years, 3D Printing has become increasingly popular as a way to reduce costs and increase production efficiency. It allows designers to create objects using digital designs by adding layers of material one at a time. So why is SLS used in 3D Printing?
ARRK Asia knows this technology is particularly useful when creating prototypes and small-scale parts, which is also great for large-scale manufacturing. For a deeper understanding, we need to explain each layer that made the advantages of Selective Laser Sintering stand out over other methods.
3D Printing & SLS
At its core, 3D Printing uses a heat source to melt plastic into layers that build up to form the final object. This process creates objects from a computer model using a variety of materials. There are two main types of 3D printers: Fused Deposition Modeling (FDM) and Stereolithography (SLA). FDM uses heated filament to deposit thin layers of plastic, whereas SLA uses light to cure liquid resin. Both methods produce high-quality results.
Stereolithography (SLA) is a 3D Printing technique where layers of liquid resin are selectively hardened using laser beams. The result is a solid object with high resolution. SLA is widely used in the medical field because it produces highly accurate implants.
SLA was developed at MIT in the 1980s. In the 1990s, researchers began experimenting with other materials, such as plastic, metal, ceramic, and glass, and discovered that they could print objects from these materials too.
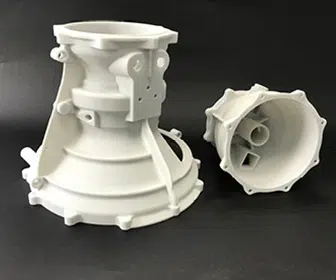
Therefore, Selective Laser Sintering (SLS) is known as a variation of SLA. Instead of using liquid resin, SLS uses powdered material. This makes it possible to create objects from various powders, including metals, ceramics, plastics, composites, and even biological materials.
SLS is often used in 3D Printing because it produces highly detailed, complex shapes. In addition, it creates stronger structures than other materials.
The materials used in this technique are a mixture of liquids and solids that are melted together at high temperatures. It is then extruded through an opening using pressure and heat. When the material cools down, it solidifies into a shape.
Selective Laser Sintering Expertise
SLS has become increasingly popular due to its ability to produce highly accurate and precise molds and dies and produce parts directly from CAD data. As a result, it enables engineers to design and manufacture components without going through costly machining processes. Furthermore, since the process does not require tooling, it is possible to produce intricate designs.
As a result, SLS has been widely adopted for use in many industries, such as Aerospace, Automotive, Electronic, Biomedical, Consumer Goods, Optics, Packaging, Robotics, and many more.
In addition to enabling Rapid Prototyping, 3D Printing products allow engineers to create new designs quickly and cheaply. This has permitted ARRK Asia to develop unique products for many companies with complex features. Contact us today to make your idea a reality!