When setting up a new project from developing a product, having the right plastic enclosure design is important, not only for a satisfying visual attribute but also for suitable usability for the end-user. There are several types of enclosures, from simple boxes to complex enclosures.
Choosing the right type of enclosure depends on many factors such as the size, shape, and purpose of the device. The choice of enclosure also affects the ease of assembly, cost, and durability. So, what kind of enclosure should you choose for your project?
Ways to select the appropriate enclosure for your project
The best way to create the perfect enclosure is by clearly defining the requirements of your product. Design around the components and find the right balance between functionality, accessibility, and aesthetics. Prototype using different rapid prototyping methods before going into production with the right design and materials.
When designing your enclosure remember to have to define the answer to the following questions:
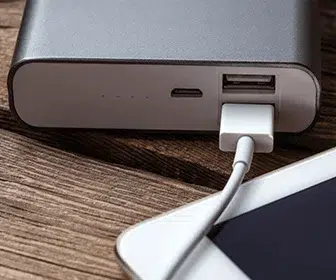
- Which shell thickness is the one your enclosure needs?
- How will it contain and organize the internal cabling and protect fragile components?
- Will the user have suitable access to the components inside if needed?
Once your team can have the answers many other details need to be taken into account, such as not forgetting to add filets, ribs, and bosses, implementing proper cooling ventilation if there will be much extra stress on the device, or adding proper clearance for each port and component in the correct usability. Creating a useful and amazing enclosure is possible when having all the right characteristics in mind.
Accessibility and Protection of components
Gluing everything together inside of the enclosure could sound like the best idea, but it takes out of the equation the characteristics of each piece the product needs to properly function.
- For accessibility: sliding faces, hinges, and screws can be easily added and combined.
- For protection: strain relief designs can reduce cable stress, and filets reduce stress on your enclosure’s corners and edges.
Some of these options require extra caution as each option can affect the tolerances of the enclosure, the placement of components, or the functionality of the product. Also, improve ergonomics and how the enclosure looks. This is why choosing the right type of material can either help or affect the lifespan of your manufactured product.
The importance of considering all details according to manufacturing requirements
A product’s power lies in its internal components but it is usually recognized by its enclosure, which makes it appealing and user-friendly. Such recognition comes from the attention to the details that improve the product for the end-user, not just for your company for its manufacturing.
As a starting point when designing anything, think about the requirements for the product. You might be surprised at how easy it is to add features later on. For example, considering such things as:
- Rounded corners can offer better quality and better visual attribute
- Avoid sharp edges when designing injection molded parts
- Reducing stress concentration with a good enclosure design
Have a good idea of what is going inside the enclosure to accurately design around it
At ARRK Asia, we fully understand the rapidly changing market demands in which many manufacturing industries can be placed. We have successfully assisted a variety of projects to ensure and meet product needs and company production lead time goals. When designing the plastic enclosure design for your project is no different.
The thickness of the enclosure’s shell is the first thing to consider when designing it, and your product development team should already know what kind of enclosure you want to make. Our team can help you in any stage you might be in need of solutions, contact us for personalized information.